Growth Champion 2025 - "La Repubblica" and "ITQF"
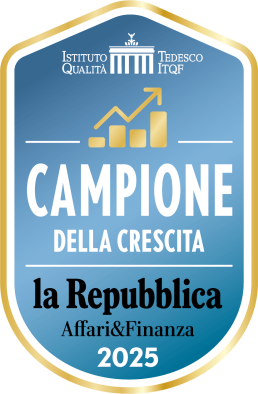
Growth Champion 2025 – “La Repubblica” and “ITQF”
TOP800 Italy, TOP80 Veneto, TOP20 Treviso
We are proud and delighted to announce that Tubilaser has been recognized as a “Growth Champion 2025” by the “German Institute for Quality and Finance” and “La Repubblica” for the four-year period 2020-2023. Our heartfelt thanks go to all of you, who are choosing Tubilaser as your partner in ever-increasing numbers. It is for you that we will continue to strive for improvement, always offering you only the very best.
Growth Champion 2024 - "La Repubblica" and "ITQF"
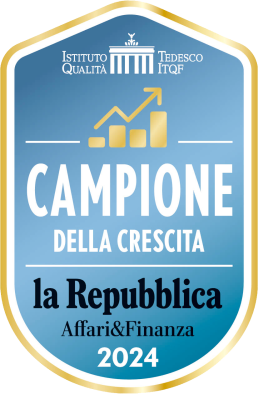
Growth Champion 2024 – “La Repubblica” and “ITQF”
TOP300 Italy, TOP25 Veneto, TOP10 Treviso
We are proud and happy to announce the recognition by “The German Institute of Quality and Finance” and “La Repubblica” as a “Growth Champion 2024” company for the four-year period 2019-2022. Thanks go to all of you who have chosen Tubilaser as your partner. Precisely for you, we will continue to improve ourselves to always offer you only the best.
Taken from “La Repubblica”, November 2023, article by Marco Fojo:
Despite the great difficulties that the economy is facing, not only nationally but globally, there is an Italy that is growing and doing so at an impressive rate. As often happens in our country, it is above all small and medium-sized enterprises that show great dynamism, thanks to their agility, flexibility and ability to innovate. And it is precisely this Italy that the German Institute for Quality and Finance wanted to photograph with its latest report entitled “Champions of growth“. Now in its sixth edition, this survey brings together eight hundred companies that have stood out for growth rates that are decidedly above average.
Read the article in full on “La Repubblica” >
Companies that are in a hurry: this is the engine of the recovery. Who are the 'Growth Champions' of the German Institute for Quality and Finance. The eight hundred Italian companies that shine in terms of turnover and employees ("Marco Frojo, La Repubblica")
Companies that are in a hurry: this is the engine of the recovery. Who are the 'Growth Champions' of the German Institute for Quality and Finance. The eight hundred Italian companies that shine in terms of turnover and employees ("Marco Frojo, La Repubblica")
New year, new machine!
We are happy and proud to announce the arrival of a new laser cutting machine! This will help to optimise productivity and prices. Send us a request to try it now!
20th year anniversary
20 years ago, along the advent of the first tube laser cutting systems in the world, Tubilaser was born.
20 years later, we want to share with you the joy and pride for this small milestone, the result of so much passion and effort.
20 years of growth based on quality and seriousness towards the customer as well as the precious experience in the laser cutting of metal profiles.
Benefits of fiber laser cutting for metal profiles, tubes, and pipes
With narrow photon beams and high-speed engines, optical fiber-based laser cutting machinery offers superior precision in the production of metal profiles and tubes.
A fiber cable conducts the laser beam to the cutting head, which is equipped with a lens system so that can focus the beam with decimal precision. Compared to CO2-based technology, fiber laser cutting offers greater efficiency, stability, and precision as well as significantly higher output. Let’s explore all the benefits of this heat-powered cutting system.
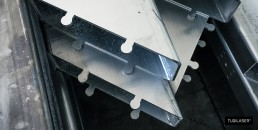
Benefits of fiber laser cutting
The most efficient and versatile laser-based cutting technology, laser cutting is suitable for processing materials such as iron, stainless steel, galvanised iron, aluminium, copper, and brass.
It allows highly precise cuts and the creation of complex geometric patterns on metal profiles of varying lengths and thicknesses, ensuring optimal results in a one-step process that minimises the need for further refinement.
With a narrow wavelength and high beam density, fiber-based laser cutting machinery penetrates materials faster and offers higher efficiency compared to CO2-based systems. On thin surfaces, the higher cutting speed results in 200% greater output.
Also, fiber laser cutting systems do not require regular source maintenance (such as reactivation or regeneration of the beam source) and ensure consistent cutting quality over time.
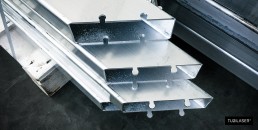
Tubilaser’s fiber laser cutting machinery
The Tubilaser production plant is equipped with 3 state-of-the-art fiber laser installations for the processing of aluminium, copper, and brass tubes and profiles up to 355 mm in diameter and up to 12,500 mm in length.
With this versatile technology, we can process highly reflective materials – such as aluminium and aluminium alloys, brass, and copper – that would otherwise damage CO2-powered cutting systems. Optical fiber systems are also suitable for processing titanium, steel compounds (such as galvanised steel, stainless steel and carbon steel), Hastelloy®, and Inconel®.
With a solid background in metals processing and advanced systems, we can cut metal profiles and tubes of any section and dimension, with maximum planning and design flexibility.
Tubilaser installations ensure high-precision cutting of pipes and profiles with exceptional finishing and minimum burrs and swarf.
Contact us today to discuss the best solution for you.
Calculate the weight of iron tubes and metal profiles with T-Cal™
Determining the weight of iron pipes, beams, and metal profiles entails complex calculations and multiple reference sources that depend on the composition and thickness of a particular piece. However, precisely calculating weight is essential to streamline a project’s design phase, reduce the purchase costs of raw materials, and ensure precise processing of units.
To help you make precise calculations, Tubilaser designed T-Cal™: a free and reliable online tool for calculating the weight of beams, pipes, profiles, and tubes made of iron, steel, aluminium, copper, and brass. To ensure maximum precision, T-Cal is based on hundreds of relevant formulas and reference charts.
This means you can determine the weight of any iron tube or metal profile (expressed as kg/m) in seconds. To calculate the weight of a single unit or batch in real time, head to the online T-Cal calculator and follow the simple three-step wizard.
How to calculate the weight of iron and metal beams with T-Cal™
- Select your material from the Materials menu.
- Select the type of tube (round, square, rectangular, or oval) or metal beam (flat, angular, U/L/H, IPE).
- Specify your item’s dimensions and click “More options” to enter the length and quantity of units/rods.
- T-Cal will automatically calculate the weight of your piece or batch.
- With T-Cal, you can also print summaries of weight calculations to attach to your projects.
Benefits of T-Cal™
With our free online tool, you can rapidly calculate the weight of tubes and pipes made of iron and other materials. This will save you time in the planning stage and beyond. Additionally, T-Cal eliminates the risk of calculation errors resulting from manual cross-referencing and provides quick and precise estimates of the weight of any single unit or batch.
For open profiles and beams (HEA, HEB, IPE), T-Cal generates a section sketch with details on thickness, spokes, and other measures that aren’t usually found in manuals and charts – but are extremely valuable in a project’s planning and processing stages.
T-Cal is used by design engineers, beams retailers, and tubes manufacturers worldwide. To access our weight calculation tool at your convenience, bookmark this page.
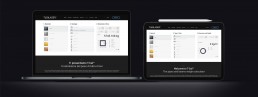
New website tubilaser.com
It’s now live our new website! We decided to renew the look, to add more content and information about Tubilaser world and in general on the laser cutting of pipes and profiles. We hope you like it and … beware of imitations! For more information on the processes click here>
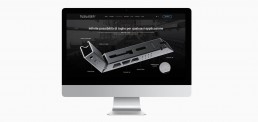
Laser cutting aluminium tubes
Laser cutting is applied when processing aluminium tubes and beams for a variety of industrial applications, such as furnishings, lighting, component production, light carpentry and aviation parts. Aluminium pipes come in all shapes and sizes, ranging from standard profile tubes (round, square or rectangular) to special profiles such as open-ended beams, flat bars, U and L profiles. Being a reflecting material, aluminium can only be cut with special optical fiber-powered lasers. Its properties may cause serious damage to CO2-powered machinery.
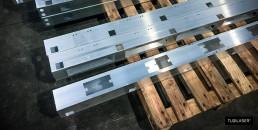
Laser cutting aluminium: benefits of fiber laser cutting equipment
The fiber laser beam is created by the seed laser and is amplified with special glass fibres. The wavelength of the power source makes the cutting faster and stronger, which means this technique is especially suitable for the processing of extra-thin or highly reflective materials such as aluminium and aluminium alloys, copper and brass.
Overall, these systems provide superior performance and benefits over CO2-based technology:
- Improved cut efficiency with identical power;
- Enhanced production speed and stability;
- Reduced energy consumption;
- Reduced machinery maintenance.
The level of precision ensured by fiber laser cutting applications of aluminium and other materials ensures the production of highly detailed and accurate finished units.
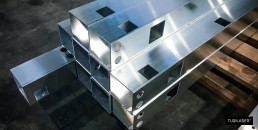
Aluminium laser cutting, without size restrictions
With tree fiber laser installations, Tubilaser can process aluminium profiles and beams without shape or size restrictions. We process round profile tubes (12 to 360 mm in diameter), long square-section pipes (12×12 mm to 250×250 mm) and rectangular pipes (20×10 mm to 300×150 mm) up to 12,5 metres long.
The flexibility of fiber laser technologies helps us meet the needs of customers tasked with challenging and extreme projects. As an example, in 2015 we laser-cut 10 m long aluminium pipes with a 250 mm diameter to manufacture street lamps to be installed in the United Arab Emirates. The contracting company had searched for a supplier in several countries, but couldn’t find anyone that could process such large profiles. Thanks to the first installation of a fiber laser prototype in the world in 2014, Tubilaser met the lighting company’s needs and provided clean-cut aluminium pipes that were used to realise the project.
Are you looking for an expert and reliable laser cutting partner for your large aluminium, copper, brass or metal beams and pipes? Get in touch today for a non-binding quote.
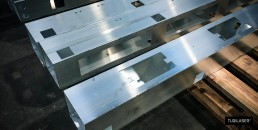
2 new laser cutting machines
Along the construction of the new headquarters, we announce the arrival of two new plants for the processing of tubulars and metal profiles.
They are extremely fast and performing, which add up to the current ones, forming a total of 6 laser cutting machines.
We constantly invest with the aim of always providing the best for our customers, strengthening the service, minimizing waiting times, managing what’s most urgent and expanding the range of sections that can be processed even to special profiles, both closed and open. Contact us for more information>
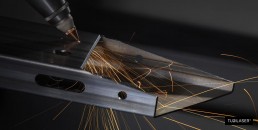
Metal processing: laser cutting
Compared to traditional mechanical systems, metal processing with laser cutting technologies provides several benefits and allows for extremely clean cuts with a +/- 0.1 mm tolerance. The superior precision of the laser cutting process minimises the need for further refining of the processed units, ensuring exceptional finishing whilst minimising burrs and swarf.
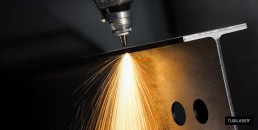
Processing metals applying laser cutting technology
Laser cutting is based on a photon beam which is aimed at the surface of the tube by a computerised system. In the context of metal processing, laser technology allows the generation of controlled high temperatures in a very small area to provoke the quickly melt or vaporise the tube surface at a specific spot.
A special nozzle located underneath the lens releases the assisting gas that creates a fluid dynamic pressure that separates and removes production debris and eliminates the need for further corrections. The geometric precision of laser combined with the purity of the assisting gas produces clean cuts with minimum surface roughness.
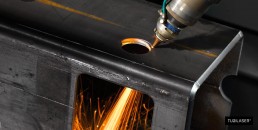
Types of laser cutting processes
Laser cutting systems vary based on the power source and assisting gas deployed during the process. Inert gas-assisted laser cutting uses gases such as nitrogen, argon and helium to remove the molten material from the cut area. This technique provides quality results with significantly reduced smearing.
The remaining types of laser cutting technologies are characterised by the used power source:
> In CO2-based laser cutting, a gas mix of electrically “pumped” carbon dioxide is used. This technology ensures metal processing of superior quality, both with standard and thick pipes made of steel or a steel alloy.
> In fiber laser cutting, a diode-based laser seed is amplified by an optical fiber system. The system enables precision processing on reflective metals such as aluminium, brass and copper.
Such technologies provide the best results for the cutting and processing of metal pipes and beams in a variety of shapes and sizes, ensuring superior cleanliness and precision compared to mechanical systems.
With two decades of experience in laser cutting of iron, steel, aluminium and other materials, we provide expert and flexible services which allows us to meet the most demanding and urgent requests applying bespoke solutions. Get in touch today for a non-binding quote.
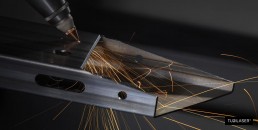